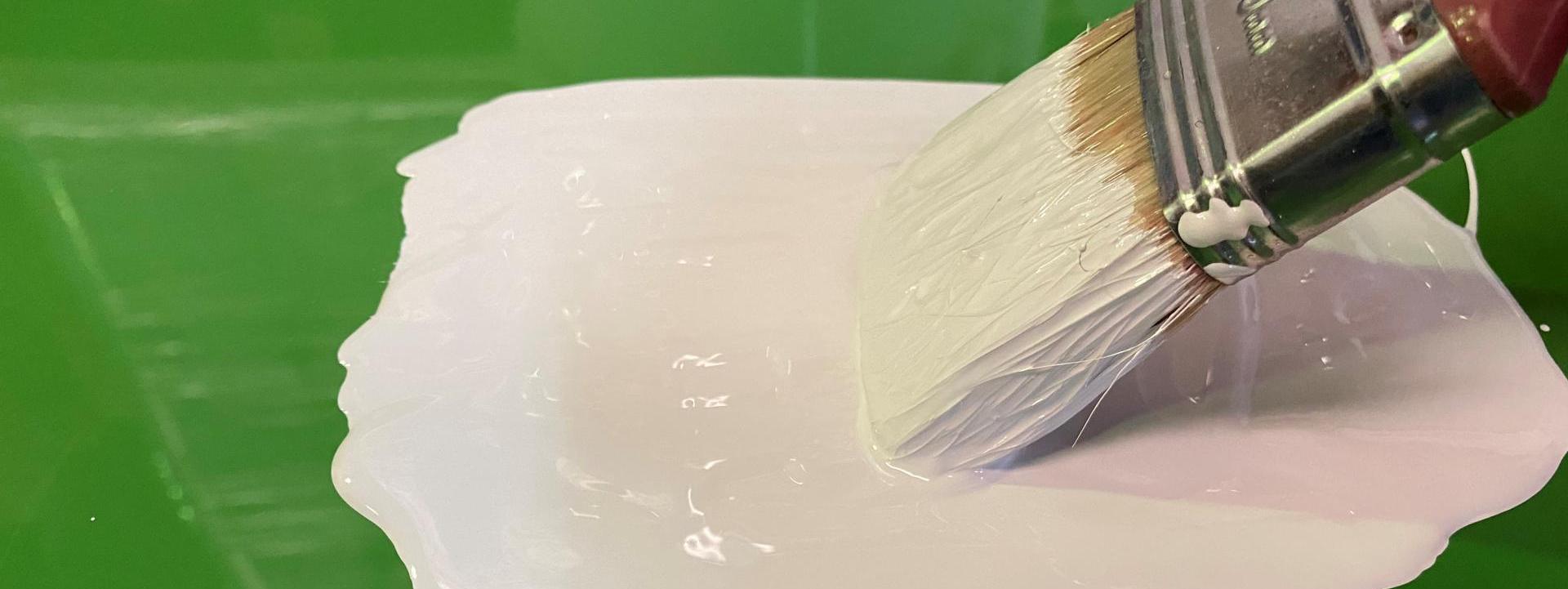
Elige el Gel coat correcto y cómo aplicarlo
Tanto si eres conocedor de lo que es un Gel coat como si no tienes mucha experiencia con ellos, en este Post queremos ayudarte a escoger el mejor Gelcoat posible para tu aplicación y a usarlo correctamente para obtener un resultado perfecto.
Elegir el correcto es fundamental para obtener un buen acabado en cualquier pieza fabricada en material compuesto (Composite).
Podemos encontrar en internet estos productos nombrados como Gelcoat y también como Gel Coat, en este post vamos a usar ambas. En el sector es aceptado de una manera u otra.
Tipos de gelcoats y sus características
- Gelcoat Industrial: la calidad más básica del mercado. En base a una Resina de poliéster Ortoftálica, con un porcentaje muy elevado de carga mineral (habitualmente carbonato cálcico). Nombrado y conocido como gel coat de poliéster. Su principal característica es su precio y su cubrición por su alto contenido en cargas. Disponible en versión brocha/rodillo y pistola. Se endurece con Peróxido de Mek. Está indicado para piezas de interior donde no sea exigible resistencia a la intemperie o cuando van a ser post pintadas. Mala retención de brillo, escasa dureza superficial y baja resistencia al rayado. HDT de 45 a 55ºC.
- Gelcoat Ortoftálico: similar al industrial. Su porcentaje de cargas es inferior por lo que mejora sensiblemente al Gelcoat Industrial. Nombrado y conocido como gel coat de poliéster. Disponible en versión brocha/rodillo y pistola. Se endurece con Peróxido de Mek. Está indicado para piezas de interior, donde no sea exigible resistencia a la intemperie o que van a ser post pintadas. Baja/media retención de brillo, poca dureza superficial y al rayado. HDT de 45 a 60ºC.
- Gelcoat Orto/Iso: aunque no es muy difundido en el mercado, es habitual que los fabricantes mezclen ambas naturalezas para tener prestaciones mixtas. Esta mezcla no siempre se especifica en la ficha técnica. Disponible en versión brocha/rodillo y pistola. Se endurece con Peróxido de Mek. Sobre todo su uso esta extendido en el sector de carcasa de pala eólica. HDT de 55 a 70ºC.
- Gelcoat Isoftálico: la calidad mas extendida en el mercado. Basado en resina Isoftálica. Cuidado, podemos encontrarlos también muy cargados. Disponible en versión brocha/rodillo y pistola. Se endurece con Peróxido de Mek. Recomendados para piezas de exterior por su resistencia a la intemperie. Buen grado de brillo, retención y resistencia al rayado. Apto para fabricar platos de ducha, piezas que están a la intemperie, barcos de gama eslora pequeña. HDT de 55 a 75ºC.
- Gelcoat Isoftálico NPG: el rey de los gelcoats en cuanto a prestaciones generales. De muy alta calidad. Su gran resistencia a la intemperie es la mas alta del mercado. El uso del Neopentiglicol en la formulación de la resina base le confiere a este Gelcoat sus cualidades de Brillo, Resistencia al rayado, Dureza Barcol, Retención del Brillo y las dos cualidades que mas lo representa, su resistencia a la osmosis y su resistencia al envejecimiento. Los fabricantes mas afamados no agregan cargas minerales en su formulación pues reducen sus cualidades. Disponible en versión brocha/rodillo y pistola. Se endurece con Peróxido de Mek. Están ampliamente recomendados en la fabricación de Piscinas, Barcos, Plato de Ducha, Toboganes acuáticos, solid surface o cualquier pieza que deba cumplir un requerimiento de alto brillo y resistencia a la osmosis y la intemperie.
- Gelcoat Vinilester: la naturaleza recomendada para fabricar los moldes rígidos en Composites, basado en resina Viniléster. Disponible en versión brocha/rodillo y pistola. Se endurece con Peróxido de Mek. Extraordinaria dureza Barcol, por encima de 50. Altísimo brillo y retención de este. Alta elongación a la rotura.
Es posible encontrar gelcoats con basados en resinas modificadas para obtener cualidades muy concretas como pueden ser con propiedades ignifugas, acabados con efecto granito o acabados de alta calidad.
Al igual que las pinturas plásticas o los esmaltes, la cantidad de colores que puedes encontrar en el mercado son casi infinitas, desde los colores de la carta Ral hasta los de una carta Pantone.
El Gelcoat blanco es el color más demandado.
Como aplico correctamente un gel coat
La aplicación de los Gelcoats es común para todas las naturalezas y calidades. Es obvio que en la fabricación de piezas con mayor valor añadido o requisitos técnicos, los parámetros de aplicación deben ser mucho mas cuidadosos. No es lo mismo pintar una pieza industrial para interior que un barco de 20 metros de eslora, donde el brillo y la resistencia a osmosis son claves.
La influencia de los parámetros de aplicación está directamente relacionada con la calidad final de la capa del gelcoat. Por ello es de suma importancia ser muy escrupulosos con las recomendaciones. La capa de gelcoat es la cara de nuestra pieza, una buenas elección de productos con una mala aplicación de ellos puede dar al traste con nuestra pieza.
Os damos algunos parámetros para que tengáis mas éxito en vuestra aplicación.
Aplicación a pistola de copa o calderín
- Boquilla: de 2,5 a 3,5 dependiendo de la viscosidad.
- Distancia de aplicación: entre 30 y 40 cm.
- Presión de aire: 3-4 bares.
- Espesor: entre 500 y 700 micras (0,5 y 0,7 mm) aproximadamente. Medir con una Galga.
- Número de pasadas: 3-4, mojado sobre mojado (wet on wet).
- Catalización: entre 1,5 y 2% de Peróxido de MEK.
- Dilución: Acetona o Estireno, sólo en caso necesario. Consultar al proveedor.
- Limpieza: Rhodiasolv Iris o Acetona.
- Temperatura de trabajo: el molde y el lugar de aplicación deben estar entre los 15 y los 25ºC. Temperaturas diferentes afectan tanto a los tiempos de trabajo, tiempos de secado como a la calidad del curado.
Aplicación pistola Airless
Aquí puedes ver un video de como se aplica un gelcoat con una maquina Airless para fabricar una piscina
Aplicación brocha o rodillo
Estas versiones de gelcoat están diseñadas para aplicarse tanto a brocha como a rodillo, NO son versiones diferentes. Dentro del conjunto de los gelcoats, el de brocha/rodillo tiene un consumo muy reducido, quizas un 10 o un 15% del mercado.
Es importante saber que la aplicación en brocha/rodillo se hace en dos pasos, es decir, debemos dar el espesor en dos partes, dividiendo la cantidad total a aplicar entre las capas y dejándolas secar entre ellas antes de aplicar la siguiente. Es muy importante que la primera sea tenga un espesor mínimo de 350/400 micras para que el Estireno de la segunda no arrugue la primera.
El sistema aplicativo sería el siguiente:
RECUERDA, debes catalizar con Peróxido de MEK y remover correctamente para homogenizar bien la mezcla.
Si quieres ampliar la información de los Composites, no te pierdas nuestros Posts.
- El Diccionario ESCUETO de los Composites
- Los Composites o Materiales Compuestos
- Gelcoats y Topcoats, que son y que puedo esperar de cada uno
Si te preguntas dónde comprar Gelcoat, en ArQuimi puedes hacerlo de manera muy fácil!!!
8 comentarios para "Elige el Gel coat correcto y cómo aplicarlo"
Deja un Comentario